Bearing of paper machine
Energy and raw material costs remain high and rising, and so are the costs associated with new health, safety and environmental legislation.Fierce competition, increasingly globalization, market forces and increasingly stringent regulatory requirements make pulp, paper and paper processing operations more difficult than ever to make a profit.
Paper mills are facing unprecedented pressure and have to focus on process efficiency, machine reliability, and all other factors that affect factory productivity and profitability, from training to information technology. RDK meets the needs of a challenging industry
RDK pulping and papermaking solutions to improve production efficiency and profitability
By combining expertise in bearings, seals, lubrication, mechatronics and services with years of experience in pulping solutions and papermaking solutions, we provide paper mills with a series of solutions that promote production and reduce maintenance needs Program.
The solutions provided cover everything from professional bearings and seals to condition monitoring technology, maintenance tools, expert consultation and binding reliability services. They help:
Increase production
Reduce downtime
Reduce maintenance costs
Reduce energy consumption and consumption of consumables
Improve worker safety
Upgrade or optimize equipment
Minimize capital expenditure
Pulping and paper industry, applications, cases, solutions
Pulping
Whether you use wood or recycled paper, the working conditions are usually wet and humid. The machinery needs to operate reliably at low to medium speeds. The range of high and low load depends on the operation.
Papermaking
The configuration of the paper machine is different depending on the products it wants to represent. However, no matter whether the paper machine is running at high or low speed, wide or narrow, their configuration must achieve higher efficiency and greater profitability.
Paper machine optimization
The problems of the paper machine will significantly reduce the agency power and quality. Provide a series of powerful solutions to overcome these obstacles. The paper machine optimization plan is specifically used to identify key equipment problems, such as the press section and carpet rolls, and is also used to collect and analyze machine status data strategically to maximize overall machine efficiency.
Medium-speed gear modification service
Older paper machines are usually equipped with medium-speed gears, and medium-speed gears often have problems when the speed of the machine increases.
Rocker arm bearing seat modification service
Rocker arm bearing seat solves the problem of drying cylinder thermal expansion that occurs when the temperature of the drying section rises. The rocker arm makes the entire bearing seat move with the shaft. However, the increased speed of the paper machine will cause vibration and rocker wear, which will affect the quality of the paper.
Asset efficiency optimization
Asset efficiency optimization combines deep knowledge accumulation, extensive industry experience, sexual services and consulting capabilities with our products and technologies. What is the final result? Fully understand your business goals and its unparalleled ability to provide you with unique solutions that create real value.
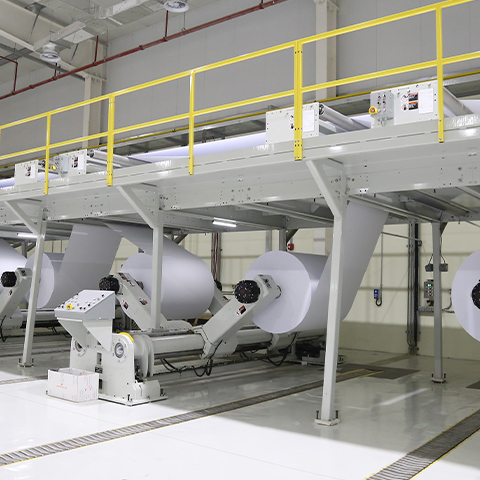