Machine tool bearing
Machine tool performance plays an increasingly important role in production efficiency and product quality. Today's machine tool customers are looking for manufacturers that can meet their high-performance requirements. To remain competitive in the market, they must provide high-speed and precise machines and solutions. Customers have the same high demand for more reliable and energy-efficient machines and components. Machine tool performance plays an increasingly important role in production efficiency and product quality. Today's machine tool customers are looking for manufacturers that can meet their high-performance requirements. RDK must provide high-speed and precise machines and solutions if it wants to remain competitive in the market.RDK machine tool solutions can help
For many years, RDK, as a close bearing product provider and solution provider in the machine tool industry, understands the technical and business challenges faced by customers, and can also see the opportunities for customers. Providing better products and solutions can help customers achieve their goals.
With deep knowledge in bearings and devices, lubrication systems, sealing, mechatronics and services, it can help machine tool manufacturers provide products and solutions with the following advantages:
Low life cycle cost
Improve the speed and precision of the machine
Increase uptime and increase productivity
Extended service life
Extended warranty
Reduce maintenance
Improve energy efficiency
Reduce environmental impact
Machine tool industry, applications, cases, solutions
Driver
To make the machine tool run efficiently and economically, the drive system components are very critical. They must have the characteristics of high reliability, high speed and high precision, while being easy to maintain and have a long working life.
Combined with these requirements, it is very challenging-the parts are not only of good quality, but also can be effectively matched with other parts.
Take electric spindle as an example, provide high-speed, sealed, ultra-precision bearings, which can be grease-free for life, with independent heavy grease device or with oil + air spindle lubrication. The sensor system used can collect valuable information about the healthy operation of the spindle, creating opportunities for greater optimization of practical processes. All drive components are optimized to provide effective lathe solutions.
Guide system
High-precision positioning and low stiffness. No stick-slip effect, ideal heat transfer effect. Guidance system solutions with these advantages can help end users obtain better guidance system performance.
Provide precision guide rails, equipped with anti-sliding system, scraper and lubrication equipment and other solutions, I wish you a hand. Such a combination can provide reliable, precise, speed and efficient operating performance-and this is just one of several guidance system solutions.
Lubrication and seals
The heat generated by friction always threatens the performance of the agent and the life of the machine tool. Various lubrication and sealing solutions to minimize the possible harm caused by heat.
These programs include customized centralized lubrication systems and automatic multi-point lubrication of drives, bearings and auxiliary equipment. Cooperate with customers to design the lubrication system according to the application conditions and optimize the type of lubricant. The same is true for sealing solutions, which include plastic and rubber seals, rotary and hydraulic seals, and can be provided in standard versions or customized.
The combination of lubrication and sealing solutions can help eliminate the risk of insufficient lubrication and overlubrication, protect the machine from pollution, and ultimately reduce maintenance and operating costs.
Measurement and monitoring
The machine operator who has the current machine performance information can take appropriate corrective measures before the machine strikes, and the money-burning, unplanned shutdown occurs. Provide several condition monitoring solutions that can help you.
Online status monitoring and fault protection system can provide early warning of machine tool spindle problems such as bearing damage, imbalance and lubrication problems. This real-time data monitoring can truly eliminate unplanned downtime, allowing operators to perform maintenance based on needs rather than schedules. An automatic data recording system can be integrated into the machine control system to record immediate shutdown or unloading.
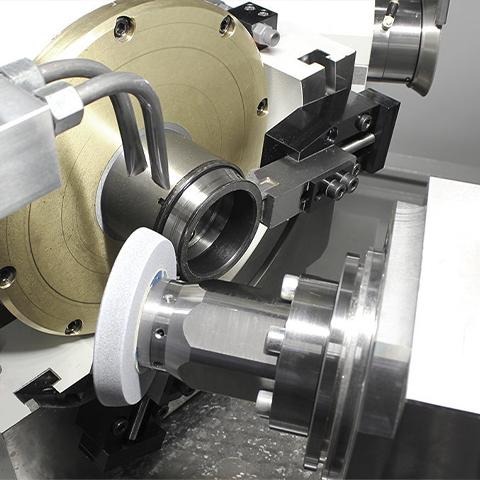